Velocity Ratio Of Gears Pdf
Illustration from Army Service Corps Training on Mechanical Transport, (1911), Fig. 112 Transmission of motion and force by gear wheels, compound train.
A gear train is a formed by mounting on a frame so the teeth of the gears engage. Gear teeth are designed to ensure the pitch circles of engaging gears roll on each other without slipping, providing a smooth transmission of rotation from one gear to the next. The transmission of rotation between contacting toothed wheels can be traced back to the of Greece and the of China. Illustrations by the Renaissance scientist show gear trains with cylindrical teeth. The implementation of the yielded a standard gear design that provides a constant speed ratio. Features of gears and gear trains include:. The ratio of the pitch circles of mating gears defines the speed ratio and the of the gear set.
Kinematics of Gears Chapter 8 Material in this lecture was taken from chapter 8 of Mott. Velocity Ratio • Without slipping there is no relative motion.
A provides high gear reduction in a compact package. It is possible to design gear teeth for gears that are, yet still transmit torque smoothly. The speed ratios of and are computed in the same way as gear ratios. 2 gears and an on a piece of farm equipment, with a ratio of 42/13 = 3.23:1 In the photo, assuming the smallest gear is connected to the motor, it is called the drive gear or input gear. The somewhat larger gear in the middle is called an gear. Download half life opposing force full rar. It is not connected directly to either the motor or the output shaft and only transmits power between the input and output gears.
There is a third gear in the upper-right corner of the photo. Assuming that gear is connected to the machine's output shaft, it is the output or driven gear. The input gear in this gear train has 13 teeth and the idler gear has 21 teeth. Considering only these gears, the gear ratio between the idler and the input gear can be calculated as if the idler gear was the output gear. Therefore, the gear ratio is driven/drive = 21/13 ≈1.62 or 1.62:1. At this ratio it means the drive gear must make 1.62 revolutions to turn the driven gear once.
It also means that for every one of the driver, the driven gear has made 1/1.62, or 0.62, revolutions. Essentially, the larger gear turns slower. The third gear in the picture has 42 teeth. The gear ratio between the idler and third gear is thus 42/21, or 2:1, and hence the final gear ratio is 1.62x2≈3.23. For every 3.23 revolutions of the smallest gear, the largest gear turns one revolution, or for every one revolution of the smallest gear, the largest gear turns 0.31 (1/3.23) revolution, a total of about 1:3.23 (Gear Reduction Ratio (GRR) = 1/Gear Ratio (GR)). Since the idler gear contacts directly both the smaller and the larger gear, it can be removed from the calculation, also giving a ratio of 42/13≈3.23. The idler gear serves to make both the drive gear and the driven gear rotate in the same direction, but confers no mechanical advantage.
Belt drives Belts can have teeth in them also and be coupled to gear-like pulleys. Special gears called sprockets can be coupled together with chains, as on and some.
Again, exact accounting of teeth and revolutions can be applied with these machines. Timing gears on a — the small gear is on the, the larger gear is on the. The crankshaft gear has 34 teeth, the camshaft gear has 68 teeth and runs at half the crankshaft RPM. (The small gear in the lower left is on the.) For example, a belt with teeth, called the, is used in some internal combustion engines to synchronize the movement of the with that of the, so that the open and close at the top of each cylinder at exactly the right time relative to the movement of each.
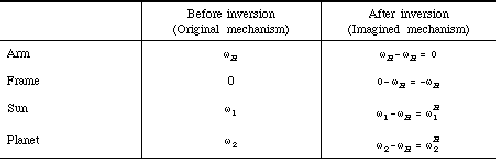
Velocity Ratio Of Gears
A chain, called a chain, is used on some automobiles for this purpose, while in others, the camshaft and crankshaft are coupled directly together through meshed gears. Regardless of which form of drive is employed, the crankshaft-to-camshaft gear ratio is always 2:1 on, which means that for every two revolutions of the crankshaft the camshaft will rotate once. Automotive applications. Main article: A close-ratio transmission is a transmission in which there is a relatively little difference between the gear ratios of the gears. For example, a transmission with an engine shaft to drive shaft ratio of 4:1 in first gear and 2:1 in second gear would be considered wide-ratio when compared to another transmission with a ratio of 4:1 in first and 3:1 in second.
This is because the close-ratio transmission has less of a progression between gears. For the wide-ratio transmission, the first gear ratio is 4:1 or 4, and in second gear it is 2:1 or 2, so the progression is equal to 4/2 = 2 (or 200%).
For the close-ratio transmission, first gear has a 4:1 ratio or 4, and second gear has a ratio of 3:1 or 3, so the progression between gears is 4/3, or 133%. Since 133% is less than 200%, the transmission with the smaller progression between gears is considered close-ratio. However, the difference between a close-ratio and wide-ratio transmission is subjective and relative. Close-ratio transmissions are generally offered in, and especially in race vehicles, where the engine is tuned for maximum power in a narrow range of operating speeds, and the driver or rider can be expected to shift often to keep the engine in its. Factory 4-speed or 5-speed transmission ratios generally have a greater difference between gear ratios and tend to be effective for ordinary driving and moderate performance use.
Wider gaps between ratios allow a higher 1st gear ratio for better manners in traffic, but cause engine speed to decrease more when shifting. Narrowing the gaps will increase acceleration at speed, and potentially improve top speed under certain conditions, but acceleration from a stopped position and operation in daily driving will suffer. Range is the torque multiplication difference between 1st and 4th gears; wider-ratio gear-sets have more, typically between 2.8 and 3.2. This is the single most important determinant of low-speed acceleration from stopped. Progression is the reduction or decay in the percentage drop in engine speed in the next gear, for example after shifting from 1st to 2nd gear. Most transmissions have some degree of progression in that the RPM drop on the 1-2 shift is larger than the RPM drop on the 2-3 shift, which is in turn larger than the RPM drop on the 3-4 shift. The progression may not be linear (continuously reduced) or done in proportionate stages for various reasons, including a special need for a gear to reach a specific speed or RPM for passing, racing and so on, or simply economic necessity that the parts were available.
Range and progression are not mutually exclusive, but each limits the number of options for the other. A wide range, which gives a strong torque multiplication in 1st gear for excellent manners in low-speed traffic, especially with a smaller motor, heavy vehicle, or numerically low axle ratio such as 2.50, means the progression percentages must be high. The amount of engine speed, and therefore power, lost on each up-shift is greater than would be the case in a transmission with less range, but less power in 1st gear. A numerically low 1st gear, such as 2:1, reduces available torque in 1st gear, but allows more choices of progression. There is no optimal choice of transmission gear ratios or a final drive ratio for best performance at all speeds, as gear ratios are compromises, and not necessarily better than the original ratios for certain purposes. See also.